Il pacchetto è arrivato! Puntualissimo e molto bene imballato. Le microfusioni della Weinert dono veramente molto belle e sono proprio soddisfatto dell'acquisto. Nella foto qui sotto, a sinistra potete vedere gli attacchi normali, a destra in basso quelli speciali, mentre a destra in alto le controrotaie.
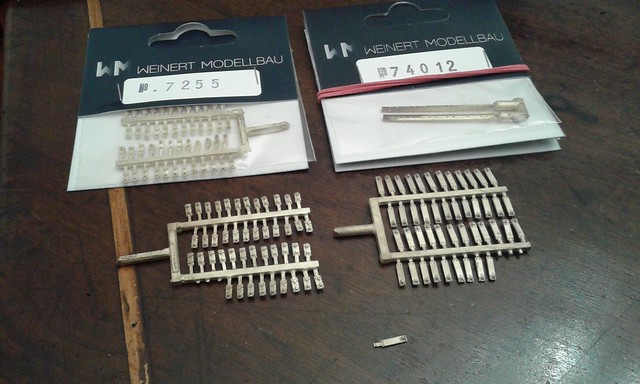
Prima però di iniziare il montaggio ho dovuto realizzare altri due strumenti da aggiungere alla solita collezione di dime et similia per la produzione dei deviatoi: una dima in due metà per i nuovi cuori, ciascuna con angolo di 5.8°, ed una dima per la produzione delle traversine.
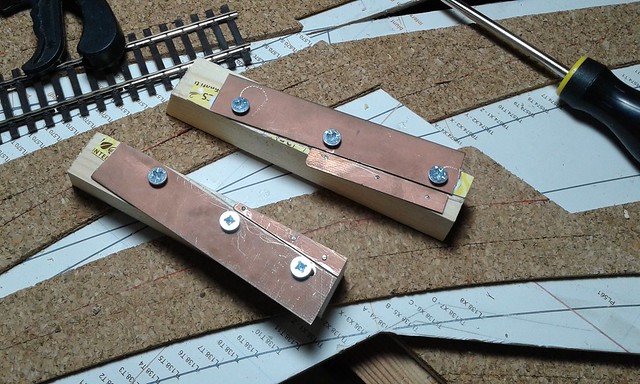
La prima dima la conoscete già, ne ho parlato qui (link); il metodo costruttivo è sempre lo stesso, soltanto ho dovuto adattare le dimensioni ai profilati di binario codice 75, alti 2mm contro i 2.5mm del codice 100. In particolare ho sfruttato alcuni resti di basetta ramata per la produzione dei circuiti stampati (PCB) spessa 1mm per fare da guida, al posto della vecchia basetta da 1.6mm. Ho anche aumentato il numero di viti da 2 a 3 per meglio irrobustire la struttura ed evitare deformazioni durante la levigatura.
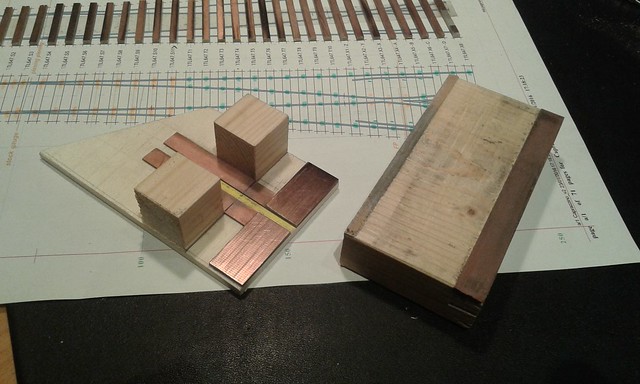
L'altra dima è anch'essa composta da due parti e mi serve per asportare il rame in eccesso sulle traversine. Questa necessità nasce da una duplice motivazione: innanzitutto estetica, volendo evitare che il rame facesse capolino da sotto lo strato di vernice che dovrò applicare per dare l'aspetto del cemento armato precompresso. In secondo luogo funzionale: infatti non solo è necessario separare elettricamente certe parti del deviatoio, ma ridurre la superficie ramata mi permette di gestire meglio il calore applicato durante la saldatura. Potete intravvedere un esempio della prima traversina finita in alto a destra nell'immagine qui sopra.
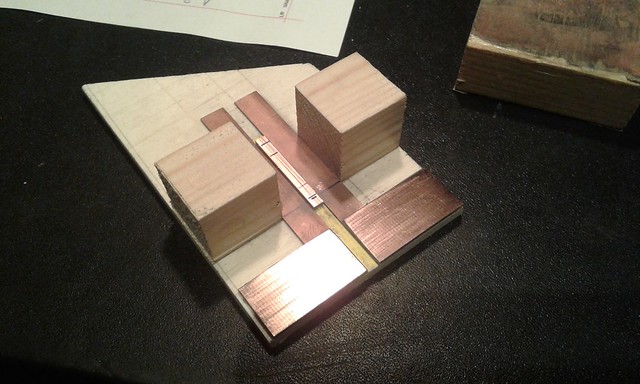
Il funzionamento è semplice: dopo avere riportato sulla traversina i limiti delle aree da conservare, la inserisco nella guida centrale realizza con due strisce di PCB spesse 1mm. Poi con un blocchetto di legno su cui ho incollato della carta vetrata asporto il rame in eccesso per abrasione meccanica.
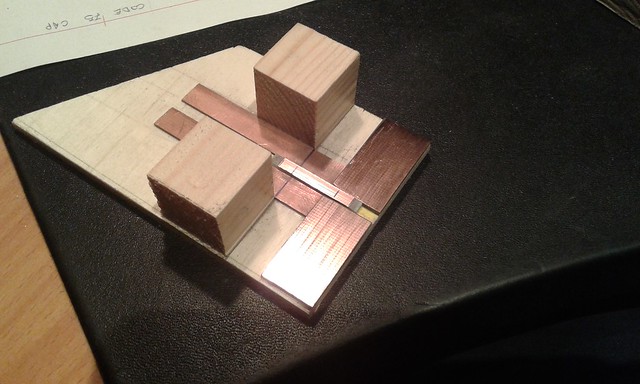
La traversina è realizzata con PCB da 2mm di spessore, quindi sporge dalla guida, ma si trova esattamente a livello con i due elementi che costituiscono la slitta. Su questi scorre il blocchetto di legno su cui ho incollato della carta vetrata, la cui larghezza coincide con lo spazio che separa la slitta dalle guide in legno. Poiché dunque legno, guida e traversina sono tutti allo stesso livello, lo spessore asportato coincide solo con lo spessore della carta vetrata. In questo modo riesco ad asportare il rame in modo uniforme e controllato, senza usare acidi o macchine a controllo numerico. Il tutto è ovviamente anche massimamente economico. Il risultato finale lo potete vedere qui sotto.
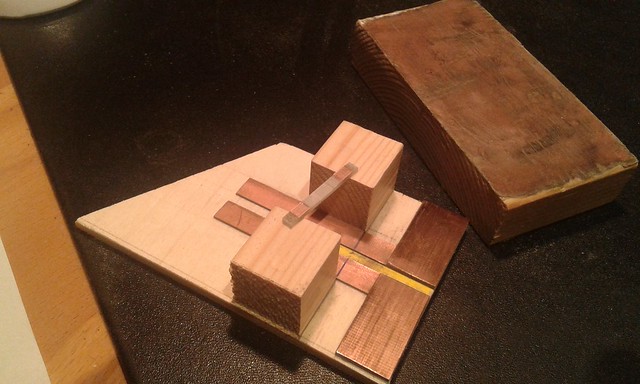
Ho già fatto anche un paio di prove di saldatura tra gli attacchi e le traversine così realizzate: dopo essermi documentato (ottimo questo link di Riccardo Olivero) ed avere fatto qualche esperimento, sono finalmente abbastanza soddisfatto. Il risultato migliore l'ho ottenuto dopo aver carteggiato leggermente le superfici di rame ed ottone con una carta vetrata con grana fine P 320 ed aver steso un leggero strato di flussante in penna (Chemtronics CW8400) che uso spesso per la saldatura dei componenti elettronici. Poi, grazie al consiglio di Enzo Carbone, ho utilizzato una minima quantità di stagno in filo da 0.2mm di diametro per saldare i pezzi fra loro.
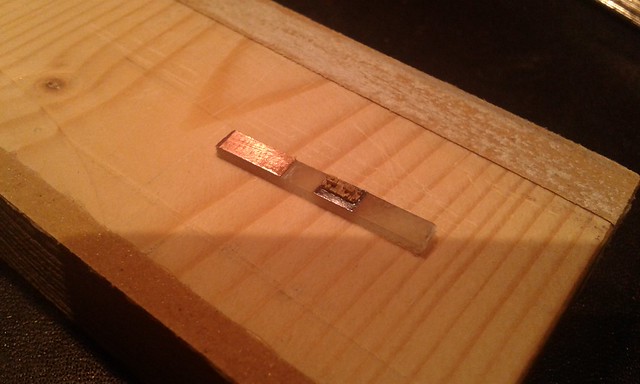
Il risultato finale è quasi perfettamente planare e molto robusto: non sono riuscito a staccarlo nemmeno tirando con una pinzetta, il che mi fa ben sperare nella robustezza dell'insieme. A questo punto ho tagliato tutte le traversine ed ho riportato su ciascuna i limiti della zona su cui andrò a saldare gli attacchi utilizzando due di questi ultimi ed il piano di posa realizzato con Templot come guida, come potete vedere qui sotto.
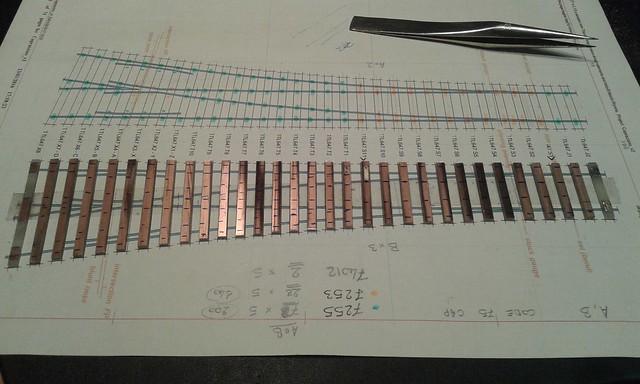
Al momento sto ancora carteggiando le traversine: le prime 8 da destra e l'ultima a sinistra sono complete, ne mancano solo altre 22...
A presto!
Nessun commento:
Posta un commento