Le vacanze di Natale, così come quelle estive, sono un periodo decisamente proficuo per avanzare i lavori su Caprazzino. Quest'anno mi sono posto come obiettivo per queste due settimane di pausa di completare il lavoro sul doppio inglese ed iniziare quello sulla nuova centrale di controllo, tanto per distrarmi un poco dalla lavorazione dei deviatoi ora che il peggio è passato.
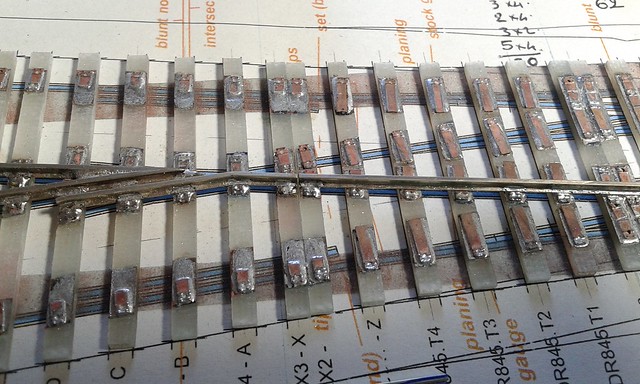
Per effettuare un lavoro per gradi e verificare che il tutto funzionasse a dovere, ho deciso di lavorare su metà deviatoio alla volta. Terminata la saldatura dei cuori ho proceduto a saldare in posizione i contraghi interni. La distanza che potete osservare in foto tra zampa di lepre e contrago è necessaria per mantenere l'isolamento elettrico. Per ridurre al minimo questo spazio, così che possa al contempo garantire un buon isolamento e non essere percepita dalle ruote dei mezzi in transito, ho utilizzato come dima un foglio di cartoncino spesso 0.5mm, come potete vedere qui sotto.
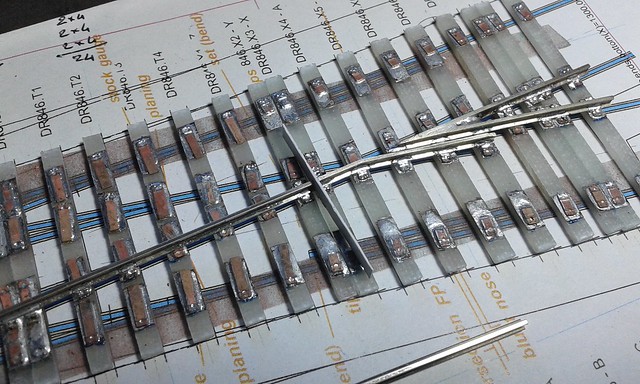
Per un posizionamento preciso ho prima saldato provvisoriamente la rotaia all'attacco più vicino al cuore, poi ho inserito il cartoncino, infine ho corretto -se necessario- la posizione del contrago. Solo a questo punto ho saldato il contrago anche ad un secondo attacco.
Lievemente diverso è stato il montaggio della coppia di aghi interni. Avendo deciso di procedere per la realizzazione di un deviatoio con aghi elastici, coerentemente con il rinnovo dell'armamento della stazione di Caprazzino, ho dovuto alleggerire il profilo della rotaia su entrambi i lati, come potete vedere dalle due foto qui sotto.
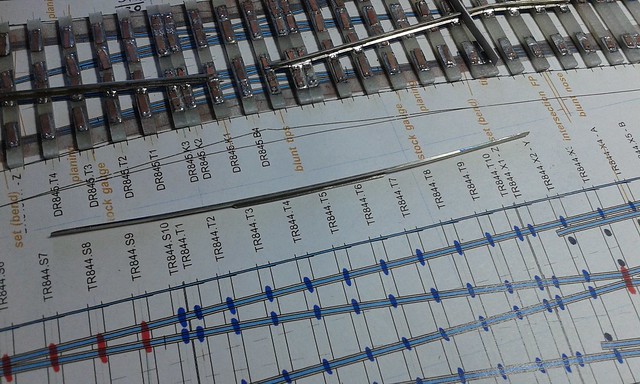
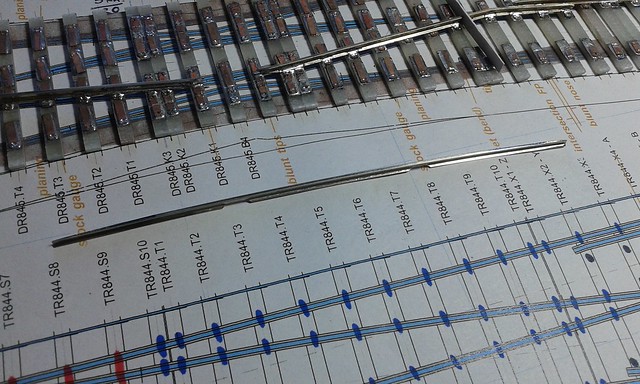
Ho fissato questo tratto di rotaia, adeguatamente precurvato per alleggerire il lavoro dei tiranti che muoveranno gli aghi, solo all'attacco al centro del deviatoio. Infatti prima di procedere con il fissaggio definitivo a tutti gli attacchi ho preferito fare qualche prova di circolazione. Ovviamente, questo significa realizzare prima tutto il deviatoio, far circolare qualche rotabile e solo a questo punto fissare definitivamente gli aghi. La scelta è dettata dall'esperienza con gli altri deviatoi già realizzati: con così tanto metallo a dissipare calore, il processo di saldatura è praticamente a senso unico. Una volta saldata una rotaia a più di un attacco, rimuoverla richiede una "certa" dose di pazienza.
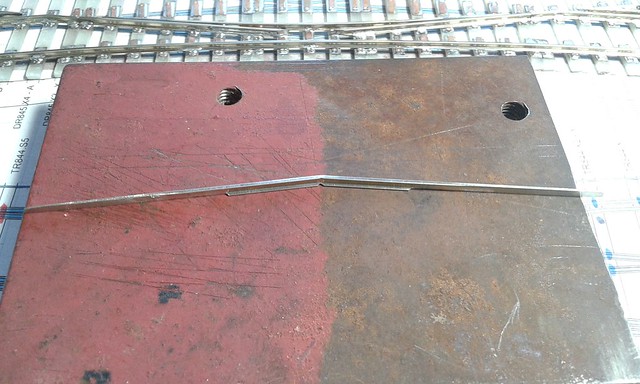
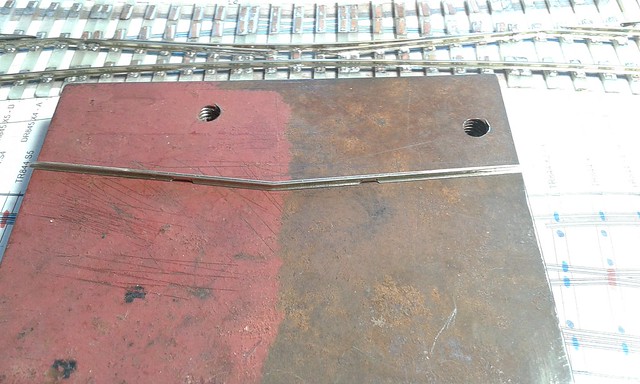
Ho seguito lo stesso ragionamento e procedimento per la seconda coppia di aghi, quelli esterni. Dopo aver montato la rotaia esterna del deviatoio, ho saldato solo all'attacco centrale la rotaia con gli aghi. Questa volta, vista la piega a 12° al centro del tratto ho dovuto fare una veloce lavorazione in più, ovvero rimuovere un tratto di piede interno in corrispondenza della piega per facilitare la lavorazione e non rischiare torsioni indesiderate sulle estremità degli aghi. Al termine del lavoro il doppio inglese si presentava così, sufficiente per una minima prova di circolazione sugli aghi esterni e sul cuore. Prova fortunatamente superata senza incidenti!
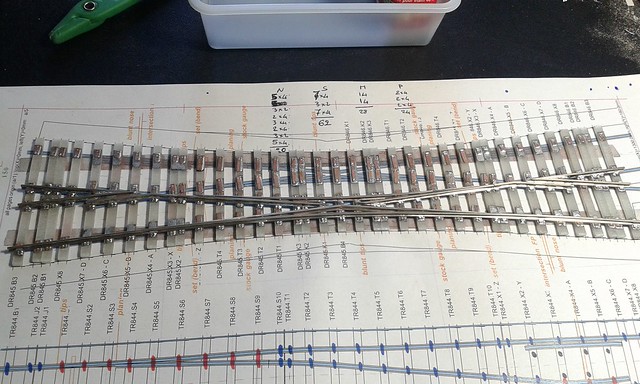
Dopo altre otto ore di lavoro sono riuscito a completare anche la seconda metà ed a condurre una prova di circolazione decisamente più seria ed esaustiva. Sebbene non fossero ancora state montate le controrotaie del cuore -sempre l'ultimo pezzo che monto in un deviatoio- ho testato tutte le possibili combinazioni di percorso e direzione con tre diversi mezzi: un carro tipo F a passo corto, un carro Kbis a passo lungo ed una vecchia MDVE Lima. Per mantenere gli aghi in posizione ho usato delle guaine di cavo elettrico poste alla base delle rotaie, tra ago e contrago.
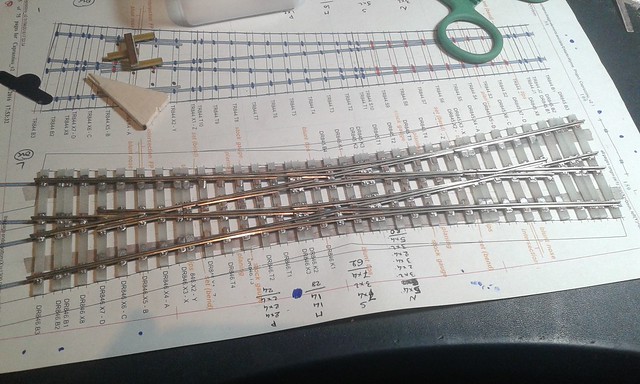
Superata anche questa prova con successo, ho proceduto a saldare le controrotaie dei due cuori. Poiché anche queste parti sono decisamente critiche per la circolabilità dei mezzi ho provveduto a saldare solo due dei sei attacchi. Ho mantenuto la corretta distanza tra rotaia e controrotaia per mezzo di una dima ottenuta con uno spezzone di traversina di risulta, assottigliato fino a raggiungere la quota prevista dalle norme NEM. Ovviamente ho ripetuto altre volte le prove di circolazione fino a che non sono stato soddisfatto del risultato. Giunto a questo punto ho saldato tutti gli attacchi e rimosso il deviatoio dal template di costruzione: qui sotto potete osservare il risultato finale. Non nego di essere soddisfatto, se non altro dell'aspetto estetico.
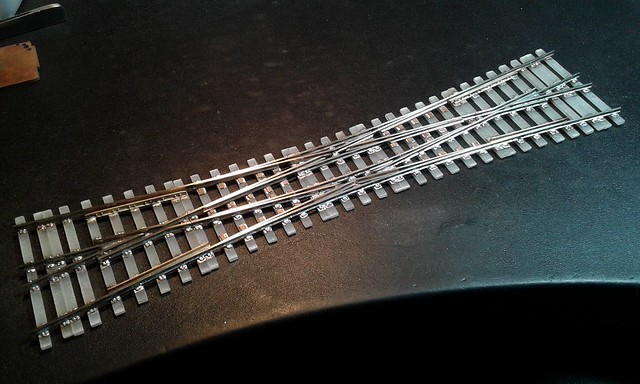
Finalmente a questo punto ho potuto iniziare il lavoro sui tiranti degli aghi. Dopo aver sagomato come da progetto i vari spezzoni di filo di rame stagnato rigido, li ho saldati alle piastrine di rame, opportunamente isolate e preforate per ospitare la barretta di comando del servocomando. Vista la complessità delle saldature, come potete vedere qui sotto, suggerisco di procedere in modo opposto al mio, ovvero saldare prima i tiranti ciascuno alla propria coppia di aghi, partendo dal più interno, e solo a questo punto saldare i tiranti alla piastrina di rame.
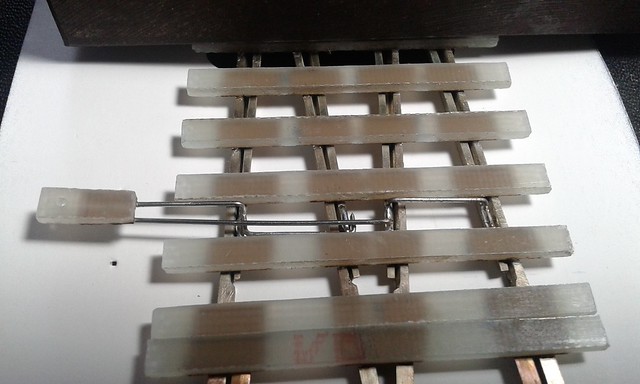
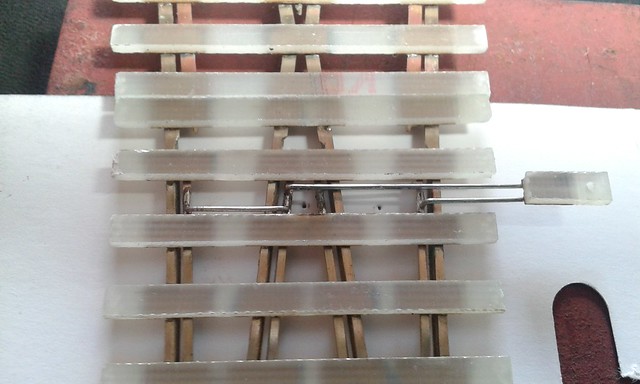
Ho ripetuto il lavoro su entrambi i lati del deviatoio: dopo aver sistemato le inevitabili imperfezioni delle prime saldature i tiranti degli aghi in posizione di riposo devono risultare paralleli e non in contatto né fra loro né con le traverse adiacenti. Inoltre, i quattro aghi devono essere tutti discosti della stessa quantità dai relativi contraghi grazie all'elasticità dei profilati metallici.
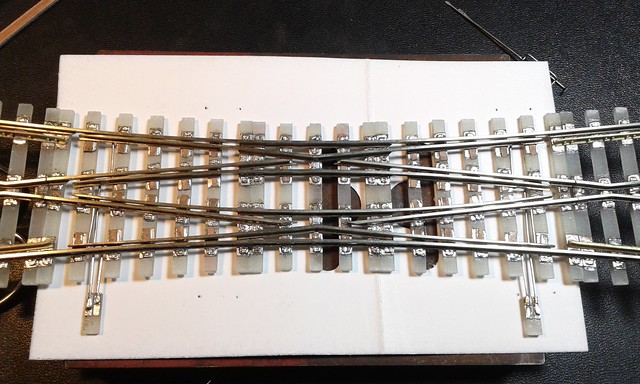
La corsa totale degli aghi risulta essere poco meno di 2mm, fortunatamente in linea con le norme NEM. Ovviamente le basette con gli attacchi verranno nascoste dalle casse di manovra.
Ora posso prendermi una pausa e dedicarmi all'elettronica.
A presto!
Nessun commento:
Posta un commento